While waiting for repair parts, and researching the possible causes for the alternator deaths… I brought over The Boy to help out with some cleanup and conversion prep.
The original flooring was actually in very good shape, other than the poor paint job applied by a previous owner. I set the boy to scrubbing it down with a high-tech degreaser and a lower tech broom. Some of the old loose paint easily came up but the rest seemed adequately adhered for the next step of the project; new flooring.
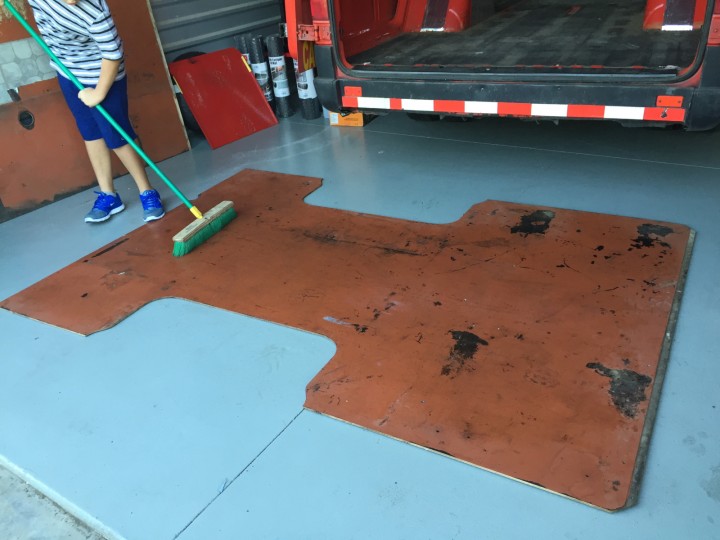
The rubber flooring I planned to use came in rolls from China, so they had been in that state for a long time. To ease installation when that phase comes around they were unrolled flat and stacked under the plywood floor. Then I found some stuff to stack on top of it to make sure they were reasonably flat.
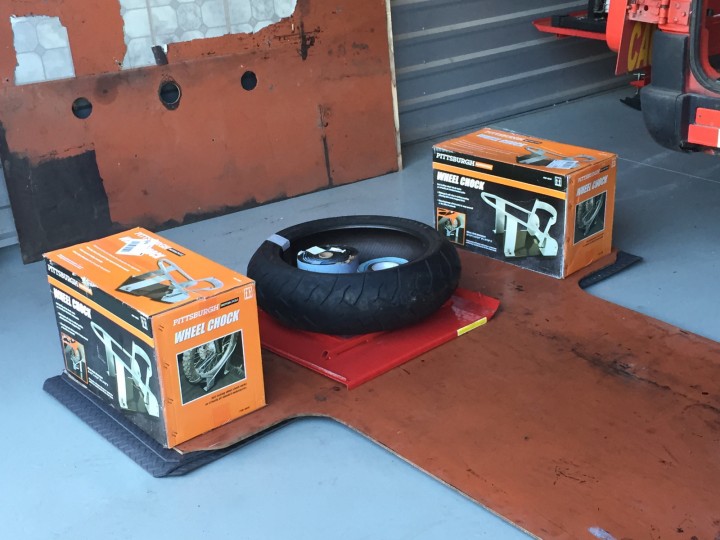
Back to the headlights… as you can see, the still need a lot of work. This is the 2nd of the pair. Again, it will be treated with sanding and polishing.
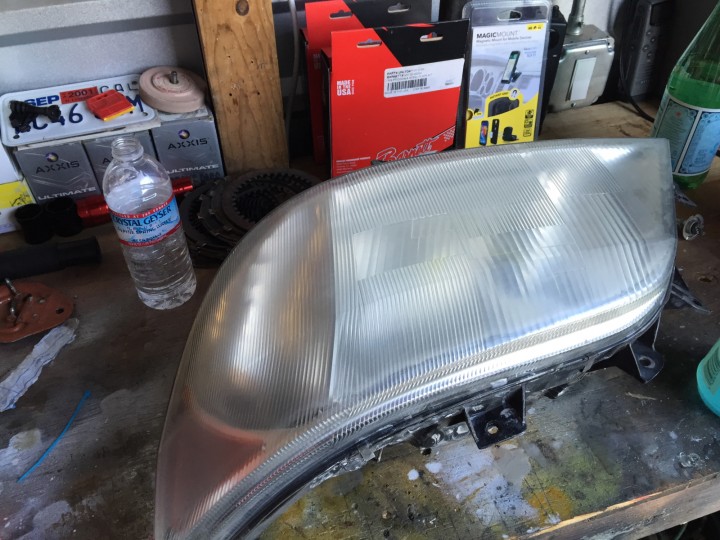
The other light is sufficiently refurbished for my needs, and was set aside during the previous day’s efforts. It doesn’t look too bad. But still not perfect. Note: I actually did one more round of this before re-installing them in the van.

Back to the interior work. Getting the road noise levels down is an important part of this projects. If I plan to do long distance treking in this, I don’t want to be yelling all day, or fatigued from the noise. I did test it with an DB meter and the average level was 85db on a highway.
Here the poor-man’s Dynomat is being installed over the wheel wells. This asphalt roof repairing product is reported to have similar sound deadening properties as the vastly more expensive Dynomat. A small roll of this is available at the local hardware box for about $16.
Using a heat gun makes short work of complex curves. Easy-peasy. It’s just a little time consuming to cut the stuff, and press it into place.
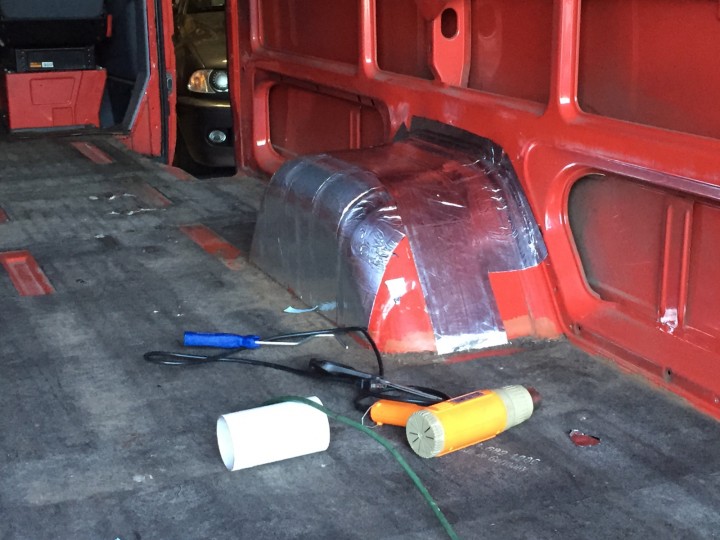
The first (and eventually failed) effort to attach the rubber to the wood. In this first round I used a Liquid Nails product. The specs looked good; very low VOCs; water cleanup… what’s not to love?
Placing pressure on the mats then maintaining with some stuff laying around the shop so that it bonds nicely to the floor. At least that was the plan I executed.
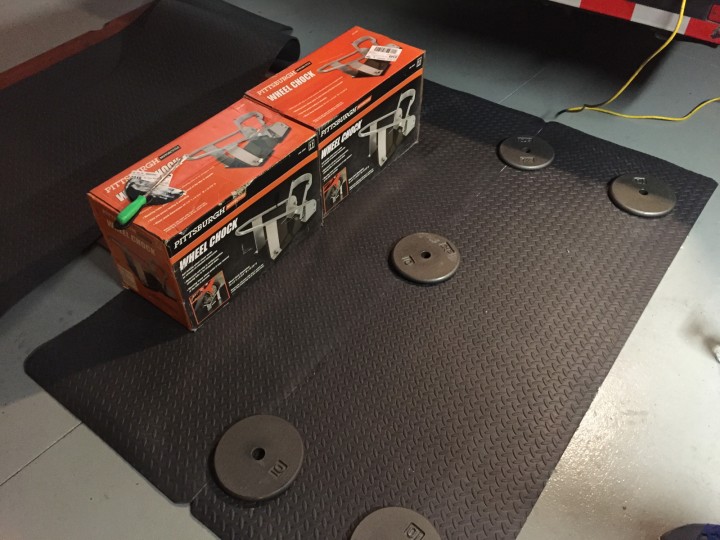
Shifting gears a little bit, I removed the Turbo Resonator and examined it on my operating room quality work area. I have a separate write-up on this. In the end I determined that the part was failing and likely contributor to the alternator death syndrome.
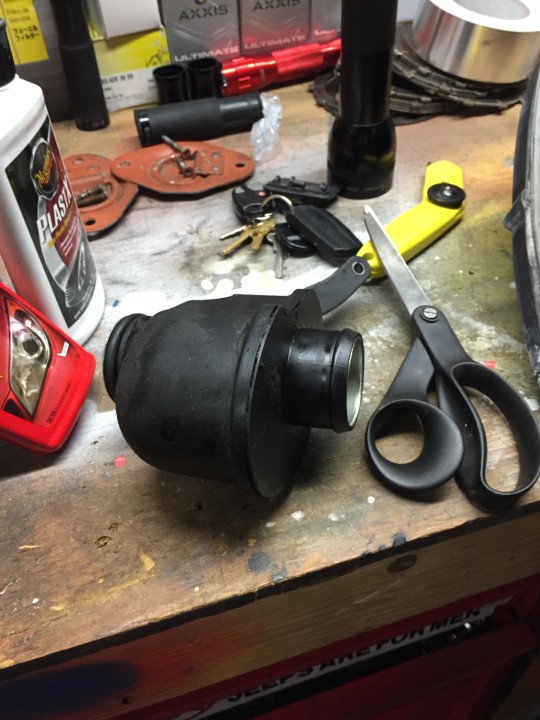
Back to the interior. With some help from The Boy we finished covering the wheel wells. The aluminum backed roofing seal didn’t fully cover the wells, so a less expensive product (Jiffy Seal) without the aluminum backing was acquired to complete the product. The Jiffy Seal was then covered with aluminum tape to maintain the same “look”.
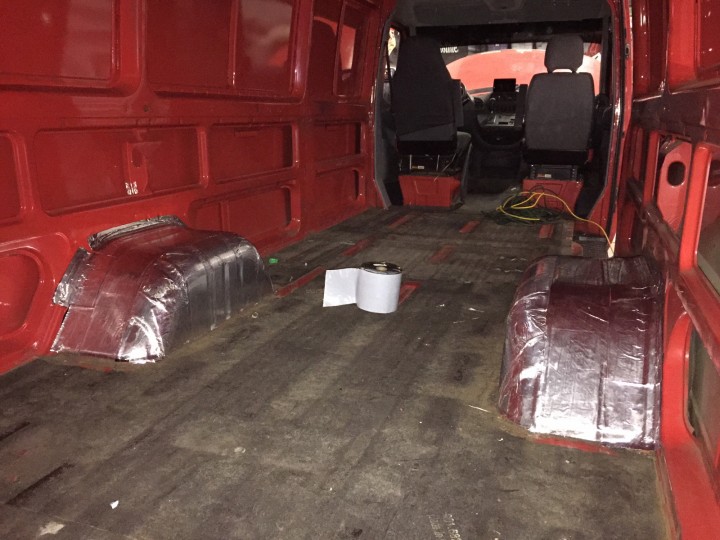
One done with the wheel wells, I popped back onto the internet to look at possible causes for the failure, the most ominous of which is a possible failure in the High Pressure injector pump (large black assembly on the right).
It does not look like a fun thing to remove and look for problems. I’m generally of the mind that if it’s not clearly broken or in need of refurbishing, I don’t want to mess with it. Some more investigation is underway.
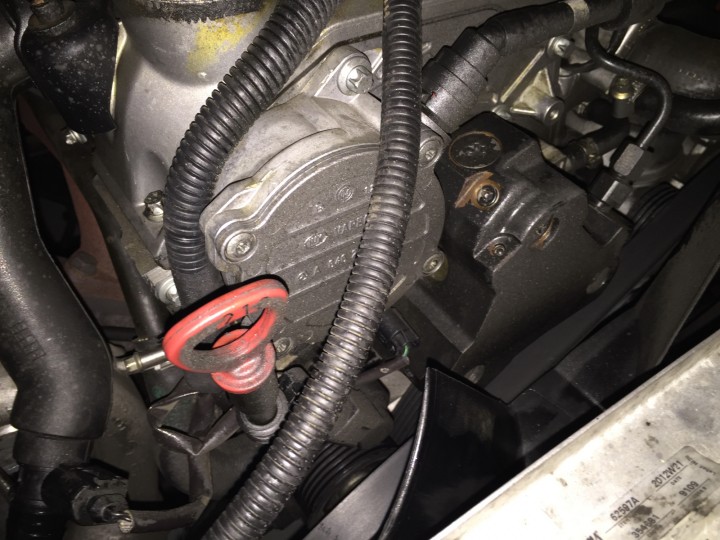
Below and to the left of the pump is the turbo charger. The intake hose as been removed and the high-pressure cold-side routing, which includes the turbo resonator has also been removed. Both the resonator and the pump are above the alternator and could possible cause it to fail should they leak fuel or high-pressure intake gasses.
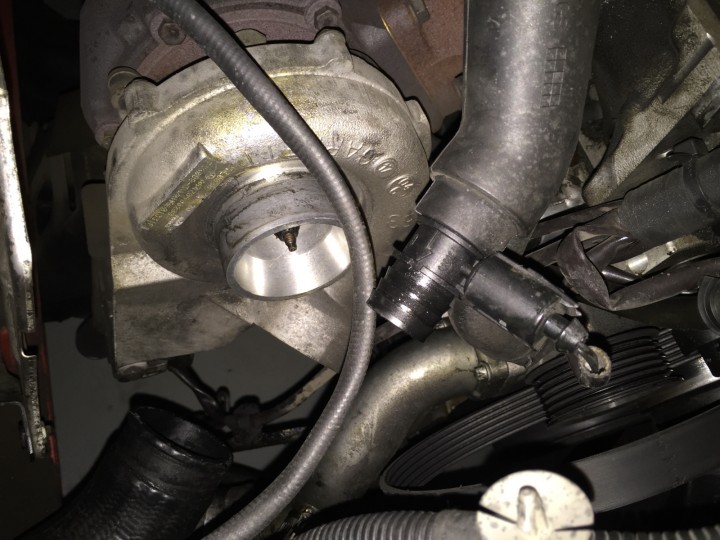
High pressure pump in close up. The black part is the front block, which bolts to a larger raw aluminum block with the drive assembly. It’s said that the pump can leak between the two plates if the bolts that hold it together, internally, begin to loosen. This is a known issue with the 2004-2006 model year.
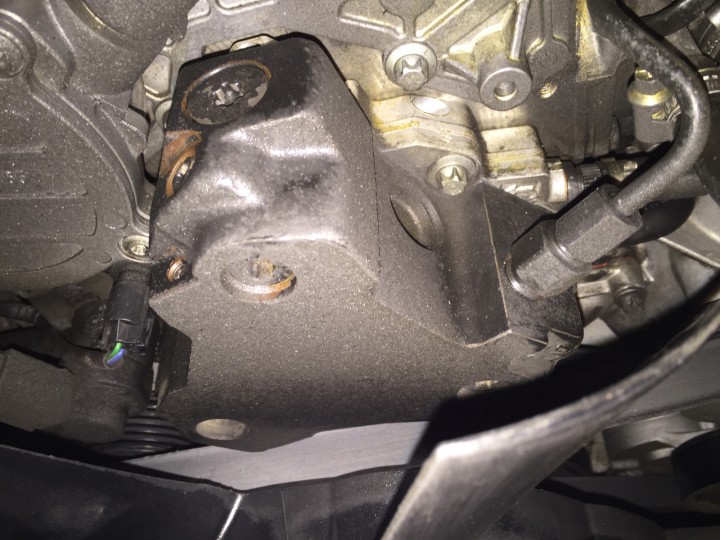
Next effort will be to consider removal of the high pressure pump. At least the front end is mostly stripped down and access will not be horribly difficult.